Dropped tools — a killer on Australian jobsites
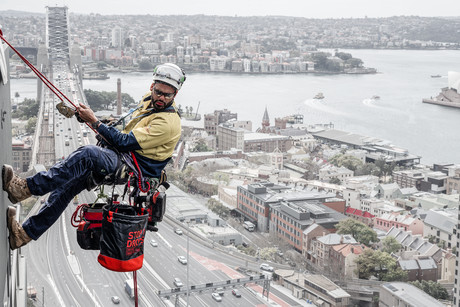
If you’re in manufacturing, construction, forestry or any of a hundred different industries, you’ve got a murderer loose in your workplace. In 2017, 15 workers lost their lives on Australian jobsites in incidents resulting from a dropped tool, with a further 16 seriously injured every working day by the same mechanism.
These objects don’t have to be large and they don’t have to be heavy — workers have suffered life-threatening and life-altering injuries from things as simple and innocuous as tape measures, spanners and bolts. Also, they don’t have to fall from high up — though many do. A fall from as low as five metres can be enough to cause traumatic brain and spinal injuries, forever changing the lives of not just the person injured, but their family and co-workers too.
It’s a problem that’s endemic in most industries — think of how many jobs involving storing, building or accessing anything heavier than half a kilogram just a few metres above head height. In recognition of this, many state/territory and national regulatory bodies have published case studies and other materials identifying the risk of dropped tools on a worksite and their potential for causing fatal injuries. Unlike workers falling from height, vehicle collision and bodily strain, there is less awareness and knowledge around the risk of dropped tools on a jobsite, with many workers provided with only the most minimal protection against tool drops. Publications such as a February 2017 WorkSafe Victoria factsheet and the Work Health and Safety (Construction Work) Code of Practice 2015 have attempted to change this, outlining the real and serious potential for bodily harm from dropped tool incidents.
Despite this, change is slow and uneven, with many workers still not provided with adequate equipment or education that could help them protect each other.
Outdated, insufficient and dangerous — current WHS requirements for preventing tool drops
While broadly Australian workers enjoy robust and comprehensive protections under a fairly extensive workplace health and safety (WHS) framework, it is not all-encompassing and does not always reflect industry best practice. For example, it has lagged behind in mandating truly effective solutions for the prevention of tool drops — making recommendations that do not take into account recent innovations in dropped object prevention.
Most state/territory and national regulators only prescribe and assess for a range of secondary preventative measures — that is, measures that only become effective once the tool has left the control of the owner. These can take a variety of forms, from debris netting to protective cages for vehicles, guardrails, toeboards and other installations meant to arrest the travel or fall of a dropped tool.
By only requiring the use of secondary measures, the risk of dropped tool incidents is merely mitigated, rather than eliminated. A dropped tool — regardless of its size, shape, travel distance and speed — is a hazard, and only intervening after the tool has left the control of the owner means that, however briefly, a hazard to the health and safety of workers exists.
Additionally, these secondary measures often only protect against certain kinds of dropped tool incidents, failing to take into account factors that commonly come into play. Wind and deflection off the structure can radically change the trajectory of a dropped tool, allowing it to strike with lethal force well outside of the vertical space below its owner. For example, debris netting can only be constructed within the jobsite — what happens if a tool falls from the 50th storey, bounces off a structure on the 45th storey and falls diagonally away from the building into the street? At this point, all safety measures have failed, and the tool is now a danger.
Old challenges, new solutions
The above raises the question: what would a truly effective tool drop prevention measure look like?
While Australia’s WHS framework continues to develop new guidelines for the prevention of dropped tool incidents, many businesses are racing ahead with their own solutions, attempting to find more effective ways to prevent injury or death on jobsites.
What sets these drop prevention measures apart is that they approach the issue of dropped tools in a fundamentally different way. They still make use of secondary measures such as barriers, exclusion zones and PPE, but they recognise that these are to be measures of last resort.
Instead, businesses are looking for ways to prevent the fall of tools at the point of origin. Rather than arresting the tool after it’s already in motion, many leading Australian construction, mining and engineering firms such as Downer Group, Rio Tinto and Lendlease Group are already making use of tool tethering systems. These systems ensure that if a worker does lose their grip on a tool, it does not fall and is instead safely caught on a small coil or tether where it can be easily retrieved without incident.
This new focus on tool tethering is aligned with risk management best practice, reflecting the priorities outlined in the hierarchy of control. This hierarchy broadly categorises methods of controlling risk according to their effectiveness at preventing injury.
At the top of the hierarchy is complete elimination of the risk — altering circumstances, designs or working practices to make the risk at hand impossible. Within the context of drop protection, elimination could be achieved by moving certain construction processes off-site or to ground level. Where this is not possible, safety managers are advised to consider substituting, isolating or engineering out the risk. Tool tethering as a practice sits between engineering and elimination — while it relies on an engineered solution and does not completely eliminate the risk as working at ground level would, it eliminates many of the factors that can lead to the creation of the event, providing more control than secondary measures such as debris netting.
However, this new approach cannot be introduced haphazardly. As with any new technology, it must be married with the proper training while being specifically targeted to that business’s precise needs. Implementing tool tethering technology without this kind of support can blunt its effectiveness, as seen in the case of a dropped tool incident in the Melbourne CBD in early 2019. The worker was using a shifter on the 25th storey tethered to his wrist, but due to a combination of factors including an overly long tether, an incorrectly chosen single-action karabiner and a lack of proper inspection by site safety officers, the tethering system failed. As a result, the tool fell over 75 metres, landing in the adjacent public street with lethal force. Fortunately, no one was struck, but the risk of fatal injury was real and present in this scenario, despite the use of a tool tethering system.
GRIPPS — the cutting-edge of dropped tool prevention
Tool tethering isn’t an off-the-rack solution. Each tool requires a unique tethering system matched to its weight, size and application — otherwise you get events like the Melbourne CBD tool drop we discussed above. This complexity is compounded by a lack of formal guidance from regulatory bodies.
While strict guidelines and standards are provided for secondary measures such as guardrails and debris netting, no such level of detail exists for tool tethering. One of the key guidance documents produced by a state or territory regulator on dropped tool incidents — the aforementioned February 2017 WorkSafe Victoria factsheet — only makes passing reference to tool tethering, limiting its comments to ‘Risk may be further reduced by use of tool lanyards’.
As such, businesses must be careful when deciding to put tool tethering into practice, as they are effectively going beyond the nice, neat prescribed solutions required by law and must develop their own responses to unique problems. Implementing tool tethering is something that must be done thoughtfully and carefully, and with proper guidance at every step.
At every step — from choosing individual products to staff education, safety checks and ongoing maintenance — you need to be ensuring that you’re making the right choice for your team. A poorly chosen, poorly applied or poorly maintained tethering system can be as bad as no system at all, so make sure that you’re providing the protection your staff needs.
To better meet the needs of Australian businesses looking to protect their staff, GRIPPS has developed the Target: Zero Drops strategic partnership program. A fully modular system, Target: Zero Drops offers a complete solution to any business looking to embrace tool tethering. With five modules to choose from, your business will have access to:
- A complete site and process audit to identify hazards and risks in current safety systems,
- A comprehensive awareness and culture program that makes your team a part of the solution,
- Certified training in dropped object prevention,
- On-site gear toolboxes and demonstrations,
- A mixture of on-site and digital safety packs that help drive the importance of proper usage,
- Post implementation audits, reviews and refresher courses.
Our extensive range of tethering products are flexible and effective, enhancing safety without sacrificing productivity. Whether scaffolding, electrical work, welding or window washing, we can provide you with the equipment you need to keep your tools and components where they belong — off the ground.
If you’re interested in embarking on the Target: Zero Drops journey with us, or want to learn more about the range of products we can provide, contact us by clicking on this link, or send us an email to conquergravity@GRIPPS.com.au
MSA LUNAR — Now live & connected in Australia and New Zealand
MSA LUNAR is a central part of the MSA Connected Firefighter Platform and is designed to increase...
MSA Cable Temporary Horizontal Lifeline
The new Cable Temporary Horizontal Lifeline (THLL) comes with multiple visual indicators that...
Head protection solutions: are you getting the maximum benefits out of your head protection?
With a good balanced fit, easy adjustment and ventilation, workers can be at ease wearing head...