Caring for safety helmets
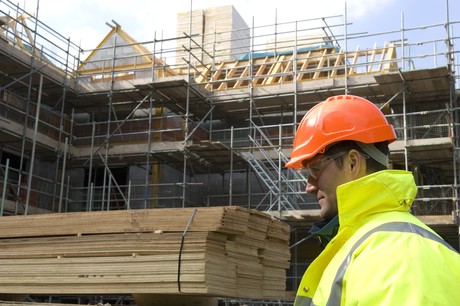
The scope of AS/NZS 1801:1997 standard specifies requirements for occupational protective helmets to protect wearers heads from falling objects in building and construction, quarrying, shipbuilding, forestry and other occupations with similar hazards. Industrial safety helmets have been designed to protect the wearer from impact and electrical hazard (up to 650 V); therefore, for the helmets to provide ongoing protection the correct care of the helmet is essential.
The design should not be modified or altered by:
- Drilling holes in the shell
- Painting the shell
- Reducing the clearance between the shell and the harness by alteration or installing objects inside the helmet
- Not using the correct harness supplied by the manufacturer
- Fitting of non-certified accessories to the helmet.
Avoid:
- Using the helmet for other than its design purpose — seats, wheel chocks, etc.
- Excessive use of chemicals such as repellents, strong cleaning agents, etc.
- Wearer alteration, eg, engraving of names, painting, fitting penholders/cigarette lighters, etc.
- The build-up of dirt, grease, etc — ensure cleaning at least weekly.
- Poor storage and unnecessary exposure to the weather and solar radiation — leaving outside when not in use or storage in the back of an open vehicle.
- Holding the cap by its brim and flexing it. This will weaken the brim and cause fatigue in the safety cap.
All these have the potential to damage or weaken the helmet and cause unseen deterioration of the shell and its harness.
Storage
Poor storage can impact on the working life of the 3M™ safety helmet. Exposure to heat, sunlight and airborne contamination can cause premature aging. It is important to ensure safety helmets are stored in an area, locker or bag free of possible damage.
Cleaning
- Wash with warm soapy water
- No harsh solvents or cleaning agents
- Use dishwashing brush for stubborn marks
- Avoid petrol, paint, adhesives and aerosol sprays
- Wash harness separately, no alterations
- Visual inspection weekly, no rough treatment
- Do not place objects between shell and harness
Mandatory head protection
Many worksites around Australia have a requirement for mandatory head protection to be worn. Industries such as mining, construction, forestry and heavy engineering can expose employees to dangerous hazards and the risk of being severely injured by falling objects, knocking your head or walking into a stationary object. The wearing of a safety helmet in these working environments is essential to worker safety.
Additional considerations
- The selection process should consider the workplace operational, occupational health and safety requirements to ensure the correct helmet type and appropriate accessories are selected.
- Ensure the wearer understands the purpose/reason for the need to wear a safety helmet.
- The wearer is instructed on the fitting and care of the helmet and/or accessories.
- Periodic inspection and maintenance is carried out to ensure the helmets are in good working condition and defective helmets and components or helmets that have exceeded a reasonable working life are replaced.
Damage
Safety helmets can endure invisible damage due to excessive exposure to sunlight, head, solvent-based paints, markers or cleaning products, or inappropriate adhesive application. 3M recommends the use of only approved adhesives. 3M also offers reflective tape and custom printing of helmets at time of manufacturing.
Comfort and correct fit
The 3M safety helmet range places wearer comfort at the same level of importance as features and performance. Learning how to adjust straps and other parts on your safety helmet for a comfortable and effective fit is essential for adequate head protection and product performance.
Multiple adjustments can be made on 3M safety helmets to personalise fit.
In fact, there are over twenty-four variations, including adjustments to allow for forehead size either moving the headband forward, back, up and down (four-way adjustment) on the four lug suspension points.
Features
- Fully compatible with our current headgear and harness.
- No screw is needed during the assembly process; the knob tightness will be consistent.
- It can be easily assembled by end user without any tool.
- Increase user comfort level with additional pad.
- Customise printing can be applied on the ratchet knob.
- Ratchet adjustment indicator.
Correct fit
To provide adequate protection to the wearer the helmet should be a comfortable, secure fit. The headband size should be adjusted to a firm but not tight fit on the wearer’s head.
- For wearers with small head sizes the head harness may need adjustment to provide a better-balanced fit.
- The peak (cap style) for general wear should be worn at the front and the cap aligned horizontally.
- The accessories selected should attach securely to the helmet and not adversely affect the balance, comfort or performance of the helmet. A helmet worn in conjunction with a visor holder and visor may require a ratchet headband to be fitted to the helmet to maximise fit security and balance.
Further considerations
Other workplace hazards may need to be considered during the safety helmet selection process.
- High noise (hearing protection) — the suitability of the industrial safety helmet to be used in conjunction with earmuffs.
- High wind areas or when used with machinery (eg, bulldozer) — the use of a ratchet adjustment headband and/or a chin strap will enhance stability.
- Eye and face hazards from flying objects, heat, splashing molten metals and chemical splash, etc — use of suitable protective face and eye shields in conjunction with the helmet (Type 1, 2 or 3) and/or the use of suitable ear and neck protectors.
- Low light (tunnels, mining, etc) — the use of suitable lamp attachments, cable clips, reflective tape and other visibility aids.
- Outdoor applications — the use of wide brim attachments, ear and neck protectors, top ventilation in the cap shell and fitting of suitable sweatbands as well as the use of light colours or high-visibility colours.
Bump caps are not an alternative to mandatory safety helmets.
- Bump caps are effective against knocks, bumps and scalp lacerations.
- Bump caps are ideally suited for some trades’ activities, domestic security, police, aviation, ground staff, transport services and auto-repair, etc.
For more information on the importance of head protection, click here: https://www.3m.com.au/3M/en_AU/safety-au/stories/full-story/?storyid=7bf10c9a-a903-469b-993c-9ab74ad1c61d.
Discover ATG®'s Industry-Leading MaxiFlex® Glove Range
Advanced Comfort, Dexterity and Protection with the MaxiFlex® Series of gloves by ATG®
MaxiCut® Ultra™ with AD-APT® - 52-4745D, 52-6745F, 52-6745FI
ATG's MaxiCut Ultra with AD-APT gloves are designed to provide exceptional cut resistance,...
Stay Cool and Comfortable with ATG's AD-APT® Technology in MaxiFlex®
ATG® has integrated its revolutionary AD-APT® Technology into the renowned MaxiFlex®...