PPE vending machines keep construction workers safe
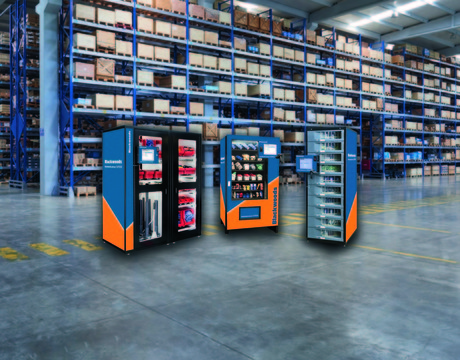
Providing the correct personal protective equipment (PPE) can be a challenge, particularly on large projects with an extensive workforce.
Maximising productivity on these kinds of large-scale construction projects demands the latest technology and equipment, as well as having it quickly made available wherever it is required.
When construction first began on the NorthConnex project in 2014, contractors Lendlease and Bouygues Construction had to find a way to supply good quality PPE to its 2000-plus workforce.
Reliability, logistics and availability of the PPE were also key considerations for the Lendlease Bouygues Construction Joint Venture (LLBJV).
Following a comprehensive audit across LLBJV construction sites, Blackwoods’ Inventory Solutions technology was selected. A series of specialised vending machines have been installed across the project sites to provide employees and contractors with 24/7 access to the latest PPE including gloves, safety glasses and masks.
Blackwoods identified opportunities to add value and improve operational efficiencies, from invoice management and cost reductions through to innovative solutions and automated product dispensary technology.
“The vending machine innovation has really benefited us in terms of time. Subcontractors can access the machines 24/7 and quickly purchase their safety equipment. Stock is replenished regularly ensuring high availability, so there is no unnecessary downtime on-site,” said Antoine Benzaglou, Purchasing Manager for Lendlease Bouygues Joint Venture.
“Safety is our number one priority, and we have very strict guidelines surrounding the types of safety products we provide to our on-site personnel.”
All PPE is checked by safety managers to ensure compliance. By supplying PPE through the vending machines, LLBJV has been able to stop subcontractors using unapproved PPE which may not meet safety standards.
The vending machines have also helped to drive down costs, particularly with a fixed price on PPE.
“We are able to accurately track and measure every single product that we use on-site, which gives us complete visibility over product usage of individual personnel,” said Benzaglou.
“The fact that the machines are automated has eliminated the need for an on-site dedicated storeman, providing another opportunity for us to focus on other tasks.”
The vending machines also consolidate total product usage by line items, reducing the administrative burden for this project.
Site personnel received extensive training on how to operate the machines so that a seamless transition to the new system could be undertaken.
“The system integrated smoothly with our ‘program’, which is mandatory when onboarding new subcontractors prior to them undertaking any work on-site. The Blackwoods team coordinated training with all our safety managers on-site, ensuring all personnel were aware of how to operate the technology and purchase PPE using their unique access cards,” said Benzaglou.
NorthConnex is a nine-kilometre tunnel linking the M1 Pacific Motorway at Wahroonga to the Hills M2 Motorway at West Pennant Hills.
Phone: 02 8873 4881
Motorola Solutions V200 body camera
The body camera is a discreet, lightweight addition to a worker's uniform. The recording...
EnableOrg AI safety software
Built by health and safety lead auditors, ISO inventors and organisational positive...
Savox Noise-COM 300 hearing protector
The Savox Noise-COM 300 hearing protector is designed to provide communication in demanding,...