Smart seed packing machine delivers greater accuracy and throughput
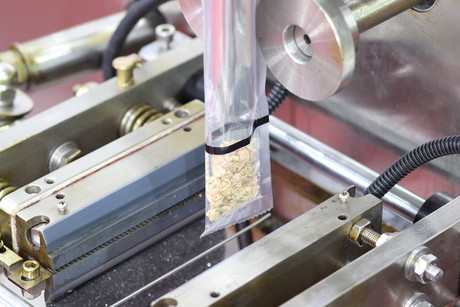
Automated seed packing machine improves flexibility and helps to reduce manual handling
As a result of the growing global population, the demand for grains, oils, and vegetables continues to increase significantly. This, in turn, is a driver for the seed market. In fact, a recent industry report estimates the value of the seed market to be USD 59.71 billion in 2018. This is expected to reach USD 90.37 billion in 2024 — a CAGR of 7.9 percent during the forecast period 2019–2024.
To meet this increased market demand, seed manufacturers are leveraging advances in automation. Addressing the challenging automation and control requirements for seed packing requires specialist knowledge and flexibility to address variations in product and packaging requirements.
By nature, the variation in product and packaging requirements has restricted the level of automation possible for seed packing. However, manual handling impedes seed manufacturers’ production capacity and their ability to meet increasing consumer demands.
Asytec — a South Australian-based automation specialist and machine builder — recognised the market opportunity and undertook the investment to develop a seed packing machine that meets global safety standards and leverages the latest automation technology and to provide a turn-key solution for seed manufacturers.
Blueprint for seed packing success
Asytec has enjoyed a long-standing relationship with Dematec Automation, a Rockwell Automation Recognised System Integrator, and therefore called on them to assist with the electrical and control system design for the automated seed packer.
Today’s seed manufacturers are challenged to deliver product to meet increased consumer demand while offering the flexibility to facilitate customised packaging to meet specific requirements regarding quantity and seed type. David Hart, CEO at Dematec Automation, knew that Rockwell Automation’s tightly Integrated Architecture solution was ideal for this application.
Operator safety is of paramount importance and the Rockwell Automation programmable safety platform enabled PLd/SIL2 Cat 3 certification to be achieved without adversely impacting on machine productivity. “The new seed packing machine was designed to automatically pack seeds of many volumes into plastic magazines, minimizing the requirement for manual handling. Therefore, the control and automation of the machine was critical to its operational success,” explained Hart.
At the core of the machine is an Allen-Bradley® control suite from Rockwell Automation operating over an Ethernet network. Primary control is delivered by the CompactLogix™ programmable automation controller with secondary control and safety provided by Micro800™ controllers. Flexible motor control was delivered by PowerFlex® 525 variable speed drives with Safe Torque-off. The PowerFlex drives provided seamless integration with the Logix environment.
“In addition to the integration and safety features provided by the solution, the flexibility of these products in the machine design helped to reduce engineering time by nearly 20 percent which is an important consideration in any OEM application,” explained Tim Bubb, managing director, Dematec Automation.
Variability and traceability
Traceability continues to present a challenge to the agricultural industry. Manufacturers are required to be able to trace seed information back to their harvest and maintain a reliable record.
Accuracy and traceability of the variety and volume of seeds going into each magazine in each trial batch is absolutely critical to achieving successful outcomes for the plant breeders. As such it is important that the integration between the system software, motion control hardware, and external database is highly accurate and reliable.
The benefit provided by the latest in intelligent software solutions is that it can eliminate the requirement for manual record keeping. The new seed packing machine utilises FactoryTalk® View to help address traceability requirements. Furthermore, FactoryTalk View provides real time visibility and receives data from a custom database that is used by plant breeders in the development of new varieties.
Smart seed-packing machine
Manufacturers can now reap the rewards from Asytec’s smart, automated seed packer. It delivers greater efficiency and reliability by providing accurate measurement, improvement in throughput and helps to eliminate packing errors. In fact, the seed packing machine has the capability to pack seeds up to five times faster and with a better standard of variety randomisation.
A key distinguishing feature of this machine is its flexibility to pack a range of seed types, using the same equipment. Asytec’s seed packing machine provides visual feedback including weight estimates and progress indication with options to override existing seed profiles. The database is dynamically updated as each seed variety is packed.
Asytec’s seed packing machine is a clear example of how automation technology can be applied to address variations in product and packaging requirements, helping to minimise human error and interaction. It helps provide seed manufacturers with the competitive edge required to stay ahead of increasing global competition.
The collaboration between Asytec, Dematec and Rockwell Automation has culminated in an industry leading OEM solution for the seed packing industry. “We have key clients looking to deploy our Seedpackers at locations around the world, which means I need the performance reliability of Rockwell Automation technology including access to their global service and support network,” said Brad Nancarrow, managing director at Asytec.
From Safety to Security: Protecting Your Machinery in the IoT Era
For decades, Pilz has been a trusted partner in safety. Now, it extends that trust to security,...
See Beyond the Visible with the BodyGuard Pedestrian Safety Warning System
Protecting employees from potential collisions is a top priority for any busy facility.
Zoomlion Crawler Crane Breaks World Record for Lifting
What does it take to break a world record?