Safe Robotics Area Protection Solutions from SICK
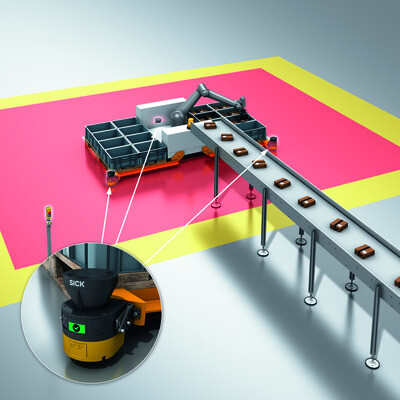
Robots have become an indispensable part of modern industry. They make it possible to flexibly adapt to changing production conditions while keeping product quality at a consistently high level. To optimally enhance the performance of humans and to increase the productivity of plants, the robotic system should ideally be freely accessible. At the same time this must not pose any risk to the health or life of the employees.
For decades, SICK’s renowned knowledge for machine safety worldwide has helped companies protect their people around machine operations effectively. These tailored complete solutions include hardware and engineering services: from planning to implementation through commissioning. The objective is to optimise the robotics applications by protecting hazardous areas in accordance with international standards.
SICK safety solutions increase productivity, enable ergonomic processes and save time and money. Safe Robotics Area Protection Solutions prevent unnecessary robot stops. An automated restart can be implemented depending on the robot application.
A solution for protecting hazardous areas around robots could, for example, consist of a combination of safety controller, safety laser scanner, and a suitably configured safety function block.
How it works
The safety laser scanner employed for robot protection uses two different field sets: one as a warning field (yellow), and one as a protective field (red). As soon as a person enters the warning field, the speed of the robot is reduced, and a dynamic adjustment of the protective field occurs. If the person enters the smaller protective field, the robot stops completely. On leaving the hazardous area, the robot will automatically restart, initially at a reduced speed then returns to its full operating speed as soon as the person has exited both the protective field and warning field.
This automated setting increases productivity, as downtimes are reduced and workflows optimised. The robot’s two-stage speed adjustment function also extends its service life.
SICK offers a variety of different solutions for protecting the hazardous area of freely accessible robotics applications. SICK can also develop, in conjunction with the customer, customised solution concepts that are tailored to the requirements of the specific robotic application.
If, for example, very little space is available, the safety experts from SICK can assist with the design of a compact and integrated solution. In this case a combination of S300 Mini Standard safety laser scanner, deTec4 Core safety light curtain, and Flexi Classic safety controller, can allow free access of the worker to the robot while minimising the safety distance to the hazardous movement.
As soon as the worker interrupts the light beams of the safety light curtain, the robot stops. The safety laser scanner in turn detects when the worker exits the hazardous area again and initiates an automated restart of the robot.
Where do I start?
The implementation of a tailored robotics solution begins with a comprehensive analysis of the actual application. The responses to the following questions provide an initial basis for understanding and correctly designing the robotics application.
- What cycle time is required for the process in this application?
- What speed is required for the robot?
- What operating modes are required for the application?
- How often does the operator need to intervene in the application?
- What hazards exist due to the movement of the robot and the processes being performed?
- Are there any space restrictions?
- What are the requirements on the range of motion and load capacity of the robot?
What are the Functional Safety Services SICK is providing?
-
Machine safeguarding evaluation
This service can identify electrical and mechanical hazards then run risk assessment of the identified hazards; it is also designed to provide evaluation of existing protective measures you have already put in place and offer recommendations of new or improvements of those measures. -
Risk assessment
SICK safety experts perform or introduce risk assessment on your request. Determine applicable directive and stands to follow, identify hazards, and conduct risk evaluation to provide specification of safety requirements according to the local standards. -
Safety concept
Provide specification of safety functions and required safety level (PLr or SILr); Provide recommendation for technical implementation of safety functions in the form of a block diagram as well as define parameters for the selection of protective devices. -
Safety hardware design
Create a SISTEMA project file and select suitable components, specify measures for controlling and avoiding systematic errors, and determine the safety level required.
From Safety to Security: Protecting Your Machinery in the IoT Era
For decades, Pilz has been a trusted partner in safety. Now, it extends that trust to security,...
See Beyond the Visible with the BodyGuard Pedestrian Safety Warning System
Protecting employees from potential collisions is a top priority for any busy facility.
Zoomlion Crawler Crane Breaks World Record for Lifting
What does it take to break a world record?