Proactive over reactive
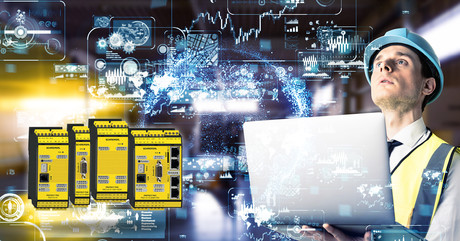
Predictive maintenance is a key component of industry 4.0, whose principal advantage can be summarised in two words: economic efficiency. To optimise machine capacity within the sense of future anticipated maintenance, a comprehensive range of data needs to be collected, beginning at the very lowest machine level. Cloud solutions support the user with the analysis and utilisation of the data.
In production that adheres to the principles of industry 4.0, the objective is not to respond to component failure reactively, but to proactively prevent the failure. Faulty components that could soon cause the plant to come to a standstill need to be identified and replaced before actual damage can occur, irrespective of the usual maintenance intervals. This is based on a system of permanent status monitoring of technical processes and components directly on the machine. Sensors measure indicators including vibration, temperature and moisture. This data is recorded and evaluated so that potential component failure can be identified before it happens.
The cloud is a key technology in this, allowing, amongst other things, comprehensive data analysis. The evaluation of monitoring information in the cloud is currently carried out with great success. The inclusion of safety technology in concepts of this nature has been an uncommon occurrence. The benefits, however, are obvious: components used to comply with safety standards can also provide data to contribute to increasing productivity.
A Safety to Cloud solution that is independent of manufacturers and systems
The Schmersal Group has for the first time introduced a Safety to Cloud solution: All safety interlocks and safety sensors as well as some safety light barriers from Schmersal fitted with an SD interface can transfer cyclical data to any cloud service via the PSC1 safety controller, an SD gateway or a separate edge gateway. A connection to this cyclical SD data within the cloud offers users comprehensive diagnostics options, including information on switching cycles, safety statuses, limit warnings, distance warnings and much more. This new solution from Schmersal is both manufacturer- and system-independent. It gives users the opportunity to freely select the cloud service that they wish to use.
System-independent formats such as OPC UA, MQTT and AMQP are available for the transfer of monitoring and status data to the cloud for customer evaluation. With the Smart Safety Solution, the edge gateway currently transfers data in MQTT format. This is an open communication protocol that has since been developed to become one of the most popular IoT standards. It is also a streamlined and cost-efficient solution characterised by easy implementation. In principle, however Safety to Cloud solutions where OPC UA is used are also a possibility. OPC UA is a pioneering standard for M2M communication protocols since it not only carries information about machines or sensors but also semantic descriptions of the information.
Visual display of diagnostics information — on tablets and similar devices
The current version of the Smart Safety Solution allows cyclical data to be saved to Microsoft Azure, for example, although the user can opt to use any cloud platform. The diagnostics information is displayed on screens. Dashboards offer a range of functions for data display, such as in the form of tables, diagrams and graphs. Using drag and drop, the user can select the data that he requires for analysing his individual processes — as an example, he can display the number of operating hours and how frequently a machine is started up. This information will then allow him to determine the anticipated component wear so that components can be replaced promptly. Data concerning operating voltage can help to identify a faulty power supply unit. Even information showing how often a safety door is opened and closed can help to draw conclusions about potential problems on a machine. Permanent data analysis in this form also gives users a much more accurate picture of their plants, and operating errors or incorrect settings can be quickly identified and rectified.
The diagnostics information can also be retrieved on mobile terminal devices including tablets and smartphones. This allows for remote monitoring of production processes and proactive deployment of service staff, such as through push notifications on smartphones, if, for example, predefined limits are reached on account of safety door offsets.
A safety solution for greenfield and brownfield plants
An additional advantage of the Smart Safety Solution is the parallel transfer of diagnostics information to the cloud with the safety functions. The secure signals are evaluated in the PSC1 safety controller so that rapid response times can also be ensured and safety functions can be reliably executed in the machine in the event of errors.
The non-secure diagnostics information, however, is not transmitted via the controller to the cloud but via the SD gateway and edge gateway, removing the need for additional development effort for the controller.
The SD gateway from Schmersal is a tried-and-tested proprietary solution for the transmission of comprehensive status and diagnostics data from safety switch gear via an SD interface. An advantage of the SD solution is the ability to connect up to 31 safety sensors and safety interlocks in series, allowing complex plants to be protected with reduced wiring effort. Legacy and existing machines (brownfield) that are protected with an SD solution can be retrofitted and existing plants can be equipped with Schmersal’s Safety to Cloud solution at a later date.
As little data as possible, as much as necessary
To limit the data volume being processed and to minimise data traffic, not all data needs to be forwarded to the superordinate level in the automation pyramid. For complex machines, designers often opt for a decentralised control architecture. The Protect PSC1 safety controller from Schmersal can be adapted by installing the PSC1-C-100 compact controller in the control cabinet and multiple decentralised expansion modules in the sub-distribution systems. In this case, the safe remote IO communication ensures the secure exchange of signals with the decentralised expansion modules. The safety controller also communicates with the controller operating the system via the universal communication interface. The operator of the plant determines which data is forwarded to the operating controller and which data is forwarded to the ERP system for further processing.
Schmersal products and solutions are available exclusively in Australia through Control Logic. Call 1800 557 705 or email sales@controllogic.com.au for more information or a no-obligation quote.
From Safety to Security: Protecting Your Machinery in the IoT Era
For decades, Pilz has been a trusted partner in safety. Now, it extends that trust to security,...
See Beyond the Visible with the BodyGuard Pedestrian Safety Warning System
Protecting employees from potential collisions is a top priority for any busy facility.
Zoomlion Crawler Crane Breaks World Record for Lifting
What does it take to break a world record?