Ensuring Safe and Secure Human-Robot Collaboration with Pilz
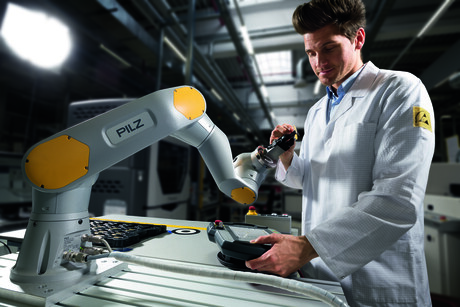
There is hardly any other machine that catches the imagination of humans as much as robots. They are the perfection of machines due to their larger degree of freedom in terms of diversity and the scope of their activities. Robots ultimately express the human aspiration to have machines that participate in people’s lives and assist them in every situation.
From cooperation to collaboration
In today’s industrial era, closer collaboration between humans and machines is on the rise. Collaborative robots, known as ‘cobots’, are designed to work alongside humans to augment and enhance performance. It keeps humans at the centre of robotic interventions. The strengths and advantages of the machines such as reliability, endurance and repetition accuracy are therefore combined with the knowledge and flexibility of humans.
Cobot applications vary significantly, but in general, they are used to extend human’s physical capabilities, enabling them to perform more high-value tasks. For example, a cobot arm could do the heavy lifting required to pick and place items, while a human performs corresponding tasks requiring dexterity and judgement. In human-robot collaborations such as these, the workspaces of the humans and robots overlap spatially and temporally.
This presents many challenges to safety as there is no one way to ensure a safe robot application. There are many aspects that need to be considered to achieve a safe and secure human-robot collaboration. Following the right processes however is key to ensuring the application is as safe as possible. Performing a detailed risk assessment of the application, implementing appropriate safeguards, followed by a thorough validation process using the appropriate measurement tools should be undertaken for all applications.
A step-by-step guide for a safe robot application
- A risk assessment is carried out at the beginning
Risk assessment involves determining the applicable harmonized standards and regulations, the limits of the machine, the risks within each life phase of the machine, the actual risk appraisal and assessment and the recommended approach to reduce the risk. It is important that each hazardous area is considered individually and without protective measures.
- The central role of validation
The safety concept and system integration are developed in a customised way based on the findings identified in the risk assessment. In contrast to risk assessment, each hazardous area is considered with protective measures in validation. For this, the robot application must be in a state such that it is ready for delivery.
In accordance with the standard, various methods must be applied for the validation, including visual checks, practical tests and measurements. Validation includes, among other things, the verification of the required performance level PLr, a fault simulation (2-channel triggering, crossfault, etc.), overrun traverse measuring if the HRC application is to be made safe using speed and separation monitoring, checking of the standards in accordance with EN ISO 10218-2 as well as collision measurement in the event of the use of the power and force limiting method.
- Touching without injuring
Collisions can be mitigated in various ways: Through design and technical protective measures such as the rounding of edges and corners and reduction of the speed of the robot movements. Finally, it must be validated by means of a measuring method whether the possible collisions are harmless from a technical safety perspective.
- Measurement of force and pressure in accordance with ISO/TS 15066
As for all measurement methods, these types of measurements must be comprehensible, traceable, and reproducible.
The Pilz Robot Measurement System (PRMS) examines human-robot collaborations (HRC), recording force and pressure.
Force measurement
The force measurement device is equipped with springs and sensors to measure the forces exerted on the human body. The nine different springs have different spring force constants and are used in force measurement to recreate the various body regions.
Pressure measurement
Pressure indicating films are used to measure the local pressure and compare it with the limit values specified in the standard. A convenient software tool is available for validating and digitalising force measurements and for generating test reports.
One can either buy or rent the collision measurement set PRMS depending on business needs. The set includes:
- 1-day practical product training including HRC measurement technique
- Force measurement device PRMS
- Pressure indicating films
- Compression elements
- Scanner for evaluating the pressure indicating films
- Sophisticated after sales package — including calibration and software updates
- Robust carry case
*Product training is included when buying the PRMS Set. When renting, the price of the product training depends on the rental period.
To date, at least, there is no one safe robot or one safe sensor technology that covers all possible scenarios from the applications in terms of safety. The requirements in relation to the safety technology always depend on the respective application. Safe robot cells only come about when everything is taken into consideration — robots, tools and workpieces as well as the associated machines such as materials-handling technology. In practice, this means that each application requires its own separate, in-depth safety-related review. The safe HRC application is therefore ultimately the result of the interaction of normative basic conditions, a complex risk assessment that is based on this, the selection of a robot with the corresponding safety functions, the selection of suitable additional safety components and, finally, validation.
As a member of the international standards body, Pilz has actively collaborated with robot manufacturers, integrators, notified bodies (such as BG) and other automation companies on the design of pioneering technical specification for human-machine collaboration in the industrial environment. Pilz also provides support for the implementation of relevant standards and directives. Jointly with the customer, the experts at Pilz work out a globally optimum safety strategy for robot applications along the life phases of the robot system through to CE marking and employee trainings which has up-to-date and practical content pertinent to robot applications.
From Safety to Security: Protecting Your Machinery in the IoT Era
For decades, Pilz has been a trusted partner in safety. Now, it extends that trust to security,...
See Beyond the Visible with the BodyGuard Pedestrian Safety Warning System
Protecting employees from potential collisions is a top priority for any busy facility.
Zoomlion Crawler Crane Breaks World Record for Lifting
What does it take to break a world record?