Ensuring the safety & accuracy of your gas detection instruments
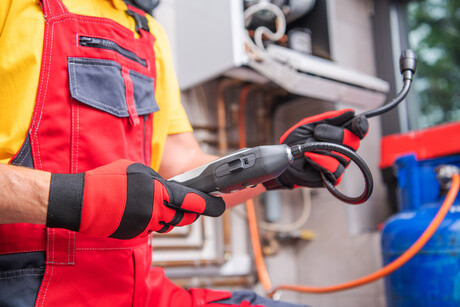
CAC GAS & Instrumentation provide calibration and bump test solutions to help ensure safety of workers through the accuracy of your personal, hand-held, vehicle mounted, or fixed gas detection instruments. Whether you require a single, disposable cylinder or a complete gas distribution system connecting multiple gas mixtures to hundreds of docking stations, CAC GAS has the solution.
As a specialty gas manufacturer, we supply calibration gas, regulators, and accessories for every gas detection instrument whether they are portable or fixed. Gas mixtures are available in a variety of sizes from 34L to more than 7500L gas volume, with gas delivery equipment, to meet your requirements.
Gas mixing and dilution systems are available that can be used for multi-point or ‘span’ calibrations for all types of instruments, even where ISO17025, ISO17034, or ‘NATA’ calibrations are required.
Our products can be used in every application where calibration gas mixtures are required.
What is Calibration?
The operation that establishes the relation, obtained by reference to one or more measurement standards, that exists under specified conditions, between the indication of a measurement system and the measurement result that would be obtained using the measurement system (source: International Vocabulary of Basic and General Terms used in Metrology).
Adjustment, done in conjunction with calibration, is when the instrument is adjusted to the correct reading while being exposed to the measurement standard.
Calibration vs Bump Testing
Bump Test
A qualitative function check where a challenge gas is passed over the sensor(s) at a concentration and exposure time sufficient to activate all alarm indicators to present at least their lower alarm setting. The purpose of this check is to confirm that gas can get to the sensor(s) and that all the alarms are functional. This is typically dependent on the response time of the sensor(s), or a minimum level of response achieved, such as 80% of gas concentration applied. Note this check is not intended to provide a measure of calibration accuracy. (ISEA)
Calibration Check
A quantitative test utilizing a known traceable concentration of test gas to demonstrate that the sensor(s) and alarms respond to the gas within manufacturer’s acceptable limits. This is typically ±10–20% of the test gas concentration applied unless otherwise specified by the manufacturer, internal company policy, or a regulatory agency. (ISEA)
Full Calibration
The adjustment of the sensor(s) response to match the desired value compared to a known traceable concentration of test gas. This should be done in accordance with the manufacturer’s instructions. (ISEA)
Why Calibrate?
To ensure your gas detector is displaying an accurate measurement, calibration is required. All gas detectors are designed to compare what is being measured to a set amount, typically a national standard (ie: LEL, etc). Over time the accuracy of the gas detector’s measurement will change (drift) due to several factors. Calibration ensures that the gas detector is not under or overestimating the concentration of gas that it is measuring.
Calibration should be done by a trained professional, at a minimum according to the manufacturer’s instructions, and data should be documented. Over time, this data will demonstrate if calibrations should be done more frequently.
Bump testing your gas detections instrument should be treated as an important part of your work routine, the same as putting on your safety boots, Hi-Vis work gear, safety glasses and hard hat. We do all these things because, at the end of the day, we all want to return home to our families safe and well.
How often should a gas detector be calibrated?
Before we can answer that, a few more questions need to be asked.
How accurate do you want your readings to be? What is the purpose of the gas measurement? What gas(es) are you measuring? All these issues play a part in answering your question. Decisions on the frequency of calibration are directly dependent upon your objectives, your application, and the gases which you are measuring.
Accuracy will be dependent upon many factors. The instrument itself (how much it drifts), exposure to gases and many other factors. Understanding your instrument: how it is used; by whom; the abuse it is taking in the field; the gases the instrument will be in contact with, will all impact your calibration frequency.
Stability data from manufacturers are based upon laboratory environments. The real world is much different, and your work environment is the key to calibration frequency decisions.
Should you calibrate more often if the instrument is used for personal safety?
Not necessarily. If the purpose of the instrument is to provide an alarm when gas concentrations increase (toxics and explosive gases) or decrease (O2), then the accuracy of the reading is not critical; meaning it is not to determine whether the concentration is 10 or 11. The instrument alarm points are set to relatively low concentrations, 5% or 10% LEL for example. An instrument which is bump/response tested daily at a value of 50% LEL will still go into alarm even if the sensor is reading 100% lower than actual. In this case it might take 20% LEL to create an alarm at 10%. This might all sound bad, but the reality is the instrument will alarm and allow the worker to leave the hazard area. Of course, you can only be sure the instrument will provide you the safety required if you have bump/response tested the instrument prior to use.
For safety purposes, if the instrument is bump tested prior to each use, then the need for frequent calibration is reduced. It all comes down to what is the purpose of the instrument.
Could your instrument be calibrated every day?
Yes, there is no technical reason why you could not calibrate your instrument every time prior to use. You can calibrate the instrument as often as you like. One large airline company calibrates their instruments every day. They do so to maximize accuracy so they can minimize risk.
The reason for not calibrating tends to be linked to not having trained personnel capable of calibrating, lack of time, and the cost. Time and cost are not an acceptable reason for not calibrating. Instruments today take little time and cost to calibrate. Calibration, though, must be completed by a trained, competent person who can calibrate an instrument correctly. This is critical, as the calibration process can change the way the instrument works. If the person uses the incorrect gas mixture or incorrect gas concentration the instrument will not work as intended.
One of the reasons docking stations have become so popular is that the device becomes the trained individual. Having said that, the docking station must still be set up using the correct calibration gas and concentration values. Whether it is a person or a machine, the system must be trained and set up correctly to achieve your goal of a properly calibrated gas detection device.
Why is Bump/Response Testing so important?
There are many reasons why your gas detector may not work correctly. Testing the instrument to a gas mixture is the only method of determining whether your gas detector is responding to a gas exposure.
Bump/Response/Function/Challenge Testing are all terms used for testing your instrument with a known concentration of test gas to determine if the instrument is working correctly and if it will respond to a gas exposure in the workplace. Typically, the instrument is exposed to the test gas while in the normal operating mode. The gas concentrations will cause the toxic and explosive sensors to increase in value and the oxygen to decrease. The user should observe this occurring with all sensors in the instrument and that the alarms (audible and visual) come on correctly. Once this is completed, the gas is turned off and the instrument allowed to stabilize. If the instrument readings do not come back to zero (toxics/combustibles) and 20.9% O2, then the instrument is normally zeroed in clean breathing air. The entire test would normal take less than 30 seconds.
You should bump test prior to every use. That includes changes of user from one part of the day to another. If your mate used the instrument this morning, you should bump test the instrument before you use it this afternoon. Your life depends on that instrument. By testing the instrument prior to each use, you are assured the instrument is working and will respond to gas exposure at that time. This does not test for the accuracy of the instrument. Bump Testing is about safety — does the instrument work and will the instrument alarm if needed.
If you want to determine whether the instrument is reading gas values accurately, then you would either calibrate or complete a verification, which we reviewed earlier. If you want both accuracy and safety, calibrate more often and bump test prior to every use.
For more on Calibration Gas Solutions for Gas Detection Instruments, visit our website to download our free eBook or contact cac@cacgas.com.au.
MSA Safety launches award-winning ALTAIR io 4 Gas Detection Wearable device
The ALTAIR io 4 and MSA+ create a versatile hardware/software combination that enhances worker...
Staying cool: The cost of heat stress in the workplace and how big fans make a big difference
High volume, low speed (HVLS) fans can help cool off employees and improve efficiency for the...
3 Elements of a Successful Gas Detection Program
Creating a successful gas detection program requires the alignment of three factors: subject...