Why material choice matters with fall arrest equipment
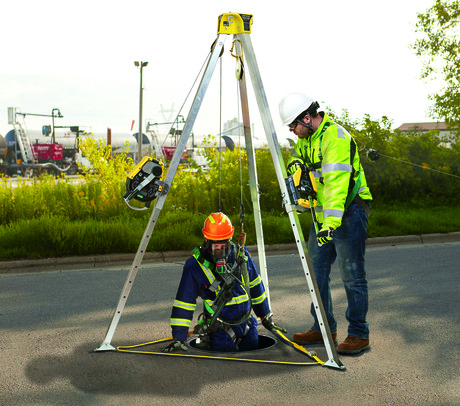
The essential attribute of personal fall arrest equipment is that it can be relied upon to arrest a fall at the first time of asking. Where lives are at stake, there should be a commitment to 100% effectiveness.
As an ISO9001 company, quality is central to all design and manufacturing procedures and is embedded into every aspect of the MSA business process.
During product development, prototypes are subjected to comprehensive testing including static strength, corrosion resistance, locking, conditioning and dynamic performance. Testing is conducted in MSA’s own laboratories to confirm compliance before the products are submitted to external laboratories for independent verification.
Understanding the environments in which height safety equipment is used informs decisions around component specification. Using marine grade 316 Stainless Steel and bronze as key materials in the internal components of our V-Series range of self-retracting devices allows for the safe and reliable operation of the units regardless of the dusty, wet or corrosive environments our products are used in.
MSA has combined premium materials with the innovation of the Radial Energy technology resulting in a self-retracting lifeline designed from the ground up to be safer, stronger and better than the older friction-brake style devices.
To understand the importance of materials in this kind of precision engineering, you need to understand the innovation.
How does the Radial Energy Absorber work?
- The absorber consists of 3 elements
- Bronze inner (moulded into the drum which houses the lifeline)
- Stainless steel brake pawl holder
- Tolerance ring (which is sandwiched in between 1 and 2).
As the webbing is pulled out/in, i.e. in normal use, all three elements rotate together.
- In the event of a fall:
- Lifeline accelerates from the PFL causing the brake pawls to extend and lock against the chassis.
- When locked the brake pawl holder and tolerance ring are stationary.
- The drum and bronze inner continue to rotate under the resistance of the tolerance ring, the energy released is then captured and contained to <6 kN.
Technological difference
The tolerance ring is a precision pre-engineered integral energy absorber, constructed of preformed stainless steel.
The profile of the tolerance ring consists of precision pre-formed ridges around its circumference.
When mated between the bronze inner and stainless steel outer (brake pawl holder) it creates a constant level of friction which maintains its consistent calibration.
The holding ability of the tolerance ring is the resultant force of all the ‘waves’ and the coefficient of friction with the mating parts. In the event of a fall, the pawl locks onto the chassis and the drum rotates independently, the friction created by the ‘waves’ of the tolerance ring between the brake pawl holder and the over moulded drum then limits the force to <6 kN.
Using the multiple wave radial energy-absorbing technology, the patented design eliminates need for an external energy-absorber outside of the housing, resulting in lighter, more robust, more efficient and reliable fall arrest solutions.
By the nature of the design the integral energy absorber requires zero recalibration or adjustment and by its nature, it is effectively sealed from external contaminants. This means industries where dust ingress has traditionally been a major issue in the use and maintenance of self-retracting lifelines is no longer a problem, allowing for safer operating and reduced service, maintenance and replacement costs.
Protection:
Precision engineering should be protected by the most durable casing. MSA V-Series self-retracting devices utilise a clear, high density, high impact resistant polycarbonate casing to protect our lifelines ensuring they work first time, every time.
Borrowing proven technologies from other industries, the polycarbonate chosen for the cases is the same used in the F-35 Lightning Joint Strike Fighter. The clear casing also proves valuable in the regular visual inspection of the units, a very useful feature designed to increase the usable life of the product. These are major considerations in the selection of key materials. It’s about changing the way we use safety equipment, enabling operators to work comfortable in the knowledge MSA has them covered.
MSA has committed extensive research and development to ensure that the right materials are used in our fall protection devices. Our V-TEC range has combined innovative engineering, superior materials and cutting-edge design to provide the most rugged self-retracting devices on the market.
Webbing:
There are two components to a webbing weave that need to be considered when determining strength, durability and UV resistance — the warp and the weft.
Warp and Weft are terms for the two basic components used in weaving to turn thread or yarn into fabric. The lengthwise or longitudinal warp yarns are held stationary in tension on a loom while the transverse weft is drawn through and inserted over-and-under the warp. Not all manufacturers of fall protection use the same blends of yarns in their webbing.
The warp in-line with the lifeline within the V-Series range of devices is HMPE (often referred to as Dyneema) and weft (perpendicular to the lifeline length) is Polyester.
Why does MSA Latchways use HMPE?
HMPE is a lightweight, high-strength synthetic fibre widely considered the worlds’ strongest. As an example of its strength, HMPE is also used in the manufacture of personal and vehicle armour and is capable of protecting people or vehicles from gunshots and IED shrapnel.
HMPE has many characteristics making it suitable for fall protection;
- Ultra-high strength versus weight (15 times stronger than steel, like for like)
- Low elongation at point of breaking
- High resistance to abrasion, moisture, UV radiation, and chemicals
- High buoyancy
- Highly flexible
- High energy absorption
- HMPE also has the highest impact strength of any thermoplastic.
HMPE can withstand significant external forces and extreme weather conditions. It is self-lubricating with a friction coefficient, is lower than nylon and comparable to that of polytetrafluoroethylene (PTFE, Teflon), but with better abrasion resistance.
MSA uses HMPE because of the above characteristics (especially its strength, abrasion resistance, excellent chemical and UV resistance), and is weaved with polyester, to increase the working life of the webbing. Polyester also has excellent resistance to UV rays and has good abrasion resistance especially when the fibre is twisted. The use of Polyester in the blend adds to this durability.
Other manufacturers use a variety of synthetic blends in their products, for example Polyester and Vectran weave for their webbing. Vectran, for example, has high strength, can withstand extreme temperatures, but its UV stability is poor — a key factor when considering the harsh Australian environment.
UV Ranking Table
MATERIAL | UV RANKING |
Polyester | 5 |
HMPE (Dyneema) | 5 |
Nylon (UV Treated) | 4 |
Aramids (Technora, Twaron, Kevlar, Nomex) | 3 |
Vectran | 3 |
Polypropelene | 2 |
Zylon | 1 |
The pedigree of HMPE in the context of fall protection lies in the use as the material of choice for technical climbing and mountaineering, having a long history providing safe anchor connections in the most extreme environments. The MSA design philosophy is centred around performance and materials selection — there is no compromise on either front.
Quality
In summary, in the design of safety equipment, compromises in the selection of raw materials leads to the inevitable compromise in safety. Work environments and the nature of some of the activities performed at height dictate that the redundancy factor PPE provides needs to have reliability as the cornerstone in the design and specification process.
MSA brings over 100 years’ experience as leaders in safety equipment design and manufacturing and have built a reputation for innovation and quality. When it comes to fall protection, this philosophy can be distilled in the statements below:
- Every element of an MSA fall protection system is designed to meet very strict design scope criteria in order for it to be deemed finally fit for purpose.
- The quality of each component is such that it can be relied upon to function correctly and arrest a fall at the first time of asking.
- Components are made of materials that have been chosen to give maximum corrosion and wear resistance and reliability in harsh environments.
- The final product meets the strictest criteria of function, usability, durability and safety.
At the end of the day, when we design fall arrest equipment, it’s about keeping your workers safe.
For more information, click here.
MSA LUNAR — Now live & connected in Australia and New Zealand
MSA LUNAR is a central part of the MSA Connected Firefighter Platform and is designed to increase...
MSA Cable Temporary Horizontal Lifeline
The new Cable Temporary Horizontal Lifeline (THLL) comes with multiple visual indicators that...
Head protection solutions: are you getting the maximum benefits out of your head protection?
With a good balanced fit, easy adjustment and ventilation, workers can be at ease wearing head...